Mastering Barcode Inventory Management Techniques
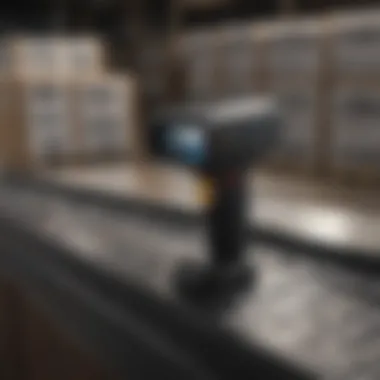
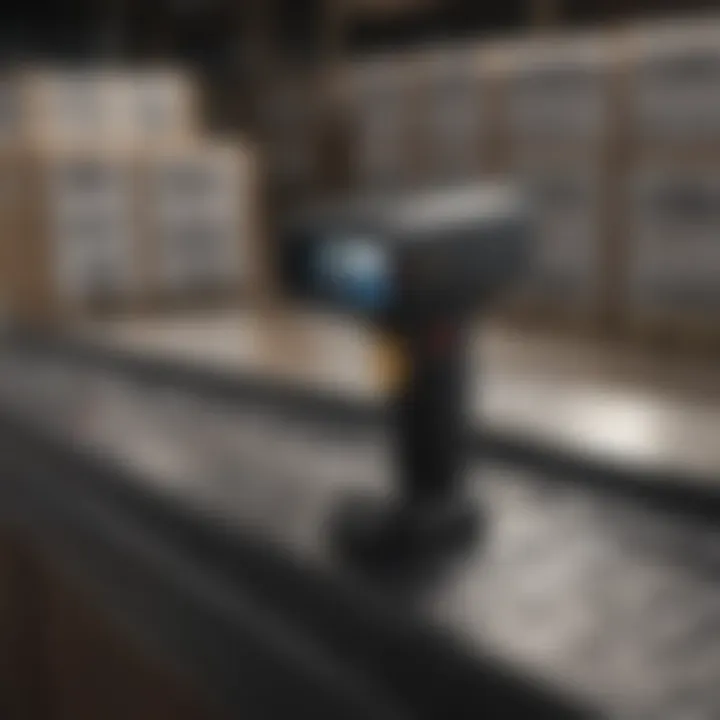
Intro
In todayās fast-paced business environment, managing inventory effectively is crucial. Companies are constantly looking for ways to streamline operations, reduce overhead, and enhance product tracking. This is where barcode technology comes into play. The application of barcodes in inventory management has revolutionized the way businesses operate. By utilizing barcodes, companies can automate their inventory processes, facilitating the smooth flow of goods from suppliers to customers.
This guide aims to explore the intricacies of barcode inventory management. From understanding the principles of barcode systems to implementing advanced techniques that boost operational efficiency, weāll cover all the bases. The content is tailored primarily for sales professionals, entrepreneurs, and startup founders who are keen on optimizing their inventory processes.
With the right knowledge in hand, small and large businesses alike can leverage barcode technology to not just manage their inventory, but to elevate their entire sales workflow.
Effective Sales Strategies
Importance of Sales in Business Growth
Sales are the lifeblood of any business. Without effective sales strategies, even the best products can languish on the shelf. The integration of barcode systems simplifies tracking sales and managing stock levels, allowing businesses to respond quickly to market demands. When you can monitor what sells and what doesnāt with precision, it not only helps in forecasting future inventory needs but also significantly reduces the risk of overstocking or stockouts.
Through effective sales practices, businesses can maximize revenue, create customer loyalty, and foster long-term growth. This is where marrying traditional sales strategies with modern technology proves vital.
Techniques for Effective Sales Pitches
Crafting a winning sales pitch requires understanding your audience and addressing their needs. Here are some techniques to consider:
- Know Your Product: A deep understanding of your product allows for confident presentations.
- Utilize Data: Leverage barcode data to show inventory turnover rates and product popularity to build credibility in your pitch.
- Tailor Your Message: Customize your approach based on the client's needs and pain points.
- Follow Up: Successful pitches donāt always result in immediate sales. Consistent follow-ups maintain engagement.
"The key to successful sales isn't just about the numbers. It's about building meaningful relationships with your customers."
Trends in Business Sales and CRM
The Role of AI and Automation in CRM
AI and automation have changed the game in sales and customer relationship management (CRM). With barcodes feeding data into CRM systems, businesses can analyze customer purchasing behaviors effectively. This data assists in creating personalized experiences that can lead to increased sales. Automated inventory tracking can also save countless hours that employees would typically spend on manual counts.
Future Predictions for CRM and Sales Techniques
Looking down the line, we can expect more integration of IoT devices with barcode systems for seamless inventory tracking. Businesses will likely harness predictive analytics to foresee trends and adapt their strategies accordingly. Those who invest in this technology today will find themselves at a distinct advantage in an increasingly competitive marketplace.
With a solid grasp of these components, you're well on your way to mastering barcode inventory management and harnessing it to drive sales effectively.
Understanding Barcode Technology
Understanding barcode technology is foundational in grasping how inventory management can be optimized. As businesses scale, the complexity of tracking products increases. Enter barcodes: a solution that simplifies this intricate task. They provide a streamlined way to monitor products in real time, drastically reducing human error and increasing efficiency.
Several important elements come into play when discussing barcode technology. These include the types of barcodes available, how they function, and the technology behind them. Itās essential to delve into these aspects for anyone looking to implement a barcode inventory system effectively.
By harnessing the power of barcodes, a business can not only cut down on the time spent on inventory management but also enhance accuracy. With the sheer volume of products that companies deal with, having a reliable method to track them becomes invaluable. Moreover, understanding the nuances of barcode technology is crucial for selecting the right tools and setting up a functional system that meets specific company needs.
What Is a Barcode?
A barcode is more than just a series of lines; itās a visual representation of data which can be scanned and interpreted by a barcode reader. Simply put, itās a machine-readable code that facilitates the automation of data entry. Youāve seen them on everything from grocery items to shipping boxes, and they serve a fundamental role in inventory management.
Barcodes generally consist of black bars and white spaces that represent numbers and letters. Each code is unique to the item it represents, providing specific information that can quickly be accessed and processed. This reliability is part of what makes them pivotal in modern inventory systems.
Types of Barcodes
Barcodes come in different varieties, each with unique characteristics suited for different applications. Understanding these types is crucial for effective inventory management.
One-dimensional Barcodes
One-dimensional barcodes, often referred to as 1D barcodes, are the traditional form of barcodes many are familiar with. They consist of a series of parallel lines that vary in thickness. These codes are predominantly used for retail, where quick scanning is essential.
The key characteristic of one-dimensional barcodes is their simplicity, allowing for quick reading by scanners. However, they can only store a limited amount of data, typically around 20-25 characters. What makes one-dimensional barcodes a popular choice is their wide availability and cost-effectiveness.
However, their primary disadvantage lies in their limited data capacity ā you won't find complex information encoded within them. For standard retail usage, though, they are more than sufficient.
Two-dimensional Barcodes
Two-dimensional barcodes, also known as 2D codes, extend beyond the limitations of their one-dimensional counterparts. These can hold significantly more data, as they use both horizontal and vertical spacing to encode information. The most recognized type of 2D barcode is the QR code; it has become common in various fields, from marketing to inventory management.
The unique feature of two-dimensional barcodes is their ability to store extensive data, such as URLs or inventory details, and they are easily scannable using smartphones. One notable advantage of 2D barcodes is their flexibility. They can be used in diverse environments and applications, making them particularly attractive for modern businesses.
Despite their versatility, thereās a caveat ā not all scanners can read 2D barcodes, and implementing them can require more sophisticated technology than what one-dimensional systems demand. This makes understanding their use; context can determine their effectiveness.
How Barcodes Work
Now that weāve established what barcodes are and their types, examining how barcodes function brings clarity to their implementation in inventory systems.
The Science Behind Scanning
The science behind scanning barcodes is quite fascinating. When a barcode scanner reads a code, it uses a laser or camera to illuminate the barcode. The variations in light reflecting off the black bars vs. the white spaces send signals back to the scanner. This signal is converted into numerical values that are then decoded into readable information.
A noteworthy aspect of this mechanic is how efficient it is ā scanning can take less than a second, drastically speeding up checkout or inventory processes.
Yet, one must consider the limitations; issues like barcode damage, poor print quality or misalignment can cause errors, leading to delays. So maintaining barcode quality is as important as setting up the system in the first place.
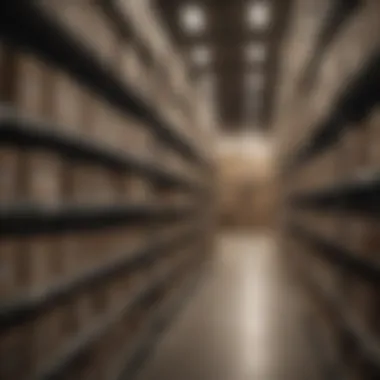
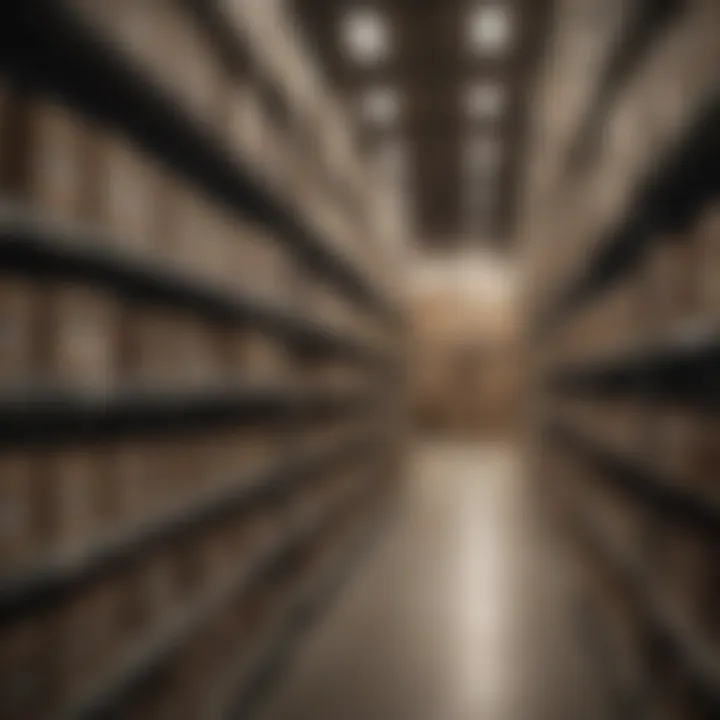
Data Encoding Formats
Data encoding formats are the backbone of how the information in barcodes is structured. Common formats include Code 128, UPC, and EAN, each serving different purposes and designed to encode specific types of data.
The key characteristic of data encoding formats is their ability to define what kind of data can be stored and how it can be interpreted. Choosing the right encoding format allows businesses to tailor the data encapsulated in barcodes according to their needs.
However, with their various standards out there, using the wrong one can complicate matters and create inconsistencies. Therefore, understanding which format aligns best with your products and operational requirements is essential for creating an effective barcode inventory system.
Benefits of Barcode Inventory Management
In today's fast-paced business environment, effective inventory management is crucial for success. Integrating a barcode inventory system offers a multitude of advantages that can significantly enhance operational efficiency. By leveraging barcode technology, businesses can achieve greater accuracy, streamline processes, and ultimately reduce costs. These benefits not only ensure smooth operations but also contribute to better decision-making processes, allowing businesses to adapt swiftly to market demands.
Increased Accuracy
One of the primary benefits of implementing a barcode inventory management system is the marked improvement in accuracy. Traditional inventory methods often rely on manual data entry, which is inherently prone to errors. With barcodes, accuracy is elevated as scanning a barcode transfers data directly into the system, minimizing the risk of human error. For example, a company managing thousands of SKUs may find that their inventory discrepancies reduce remarkably when barcodes replace manual counting.
Furthermore, the precision with which data is collected allows for better tracking of stock levels and locations. This means that when a customer checks on stock availability, the information returned is not only reliable but also up-to-date. Clarity like this builds customer trust and promotes streamlined operations.
Time Efficiency
Time wasted on stock checks and order management can be a heavy burden on any business. The implementation of barcodes reduces the time it takes to process data related to inventory. Employees will find that scanning items is much swifter than entering information manually.
For instance, consider a warehouse where staff must frequently check inventory levels. Using a barcode scanner, they can complete their tasks in a fraction of the time. This efficiency not only enhances employee productivity but also frees up valuable time that can be used for more strategic tasks, allowing businesses to operate at a higher level.
In addition to speed, barcode systems also help in optimizing reorder cycles. By utilizing real-time data, businesses can prevent stockouts or overstock situations, ensuring a well-balanced inventory that meets customer needs.
Cost Reduction
Adopting a barcode inventory system translates to notable cost savings in various areas. Firstly, the reduction in errors directly correlates to fewer returns and replacements, which can drain a company's profits. Moreover, when inventory is managed accurately, businesses can better forecast demand and make informed purchasing decisions, ultimately avoiding overstock and surplus issues.
Thereās also the potential for improved labor cost management. Since barcode systems streamline inventory tasks, fewer personnel resources may be needed to handle the same volume of work. This not only leads to a reduction in payroll expenses but also allows the existing workforce to focus on higher-value activities where human insight is essential.
In summary, the benefits derived from barcode inventory management are substantial and multifaceted. With increased accuracy, enhanced time efficiency, and considerable cost reductions, itās clear that embracing this technology can propel a business forward.
"Barcode technology isn't just a trend; it's a standard of operational excellence that more businesses should adopt."
Overall, implementing a barcode inventory management system lays a solid foundation for companies eager to improve their operational capacities and respond dynamically to the ever-changing market landscape.
Setting Up a Barcode Inventory System
Establishing a barcode inventory system is a cornerstone for any thriving business and plays a pivotal role in enhancing operational efficiency. It streamlines various processes, making inventory management less of a headache and more of a breeze. The primary focus here revolves around understanding inventory needs, selecting the right software and hardware, and ensuring effective implementation. Each of these elements contributes to an overarching goalāoptimizing the way businesses handle their stock.
Assessing Your Inventory Needs
Identifying Inventory Types
One of the first steps in setting up a barcode inventory system is identifying inventory types. This means taking a hard look at what you're actually working with. Different products require different tracking methods, which is where this aspect shines. For instance, perishables may need more frequent scanning compared to non-perishables. Such distinctive characteristics make identifying inventory types a vital component of inventory management.
- Key Characteristic: It helps categorize products.
- Why Beneficial: Effective classification streamlines processes down the road.
- Unique Feature: This can incorporate various goods ranging from clothing to electronics, allowing businesses to tailor their systems as needed.
The main advantage here is that it offers a more organized structure, preventing chaos. However, the flip side could be that it necessitates time and attention upfront, but trust me, it pays dividends later on.
Determining Inventory Size
Following the identification of inventory types, the next logical step is determining inventory size. The dimension of your stock fundamentally shapes how the entire system operates. Smaller businesses might need basic solutions while larger entities may require intricate setups.
- Key Characteristic: It gauges scalability and resource allocation.
- Why Beneficial: Aligning your system to your size prevents overwhelm and inefficiency.
- Unique Feature: This involves understanding seasonal fluctuations in demand, which can directly impact how you manage stock.
Knowing your inventory size has its advantages, particularly in financial forecasting and avoiding overstock situations. However, misjudging this can lead to either excess costs or stock shortages, thus creating a balancing act.
Choosing the Right Software
Cloud-Based Solutions
When it comes to selecting software, cloud-based solutions are becoming ever more popular. These options allow users to access their inventory systems from virtually anywhere, which aligns nicely with the increasingly mobile work environment.
- Key Characteristic: Accessibility across multiple devices.
- Why Beneficial: It fits for businesses of all sizes, providing flexibility without the fuss of managing local servers.
- Unique Feature: These solutions typically offer automatic updates, ensuring your operations remain current.
Despite advantages, a possible downer might be reliance on an internet connectionālose that connection and so too does access to your system. Nevertheless, the benefits often outweigh the drawbacks.
On-Premise Software
On the flip side, on-premise software provides a more traditional route. This option requires installation on local computers, offering a localized solution that works well for organizations that prioritize control over their data.
- Key Characteristic: Full control over systems and data.
- Why Beneficial: This can offer enhanced security and customization tailored to specific business needs.
- Unique Feature: Local installations can sometimes deliver faster performance as they are not dependent on internet bandwidth.
However, one major point to consider is that maintenance is your responsibility. Costs for IT support can stack up. Still, for some businesses, this level of control feels reassuring.
Selecting Barcode Hardware
Barcode Scanners
No barcode inventory system would be complete without discussing barcode scanners. These devices are essential for reading the barcodes. They vary from handheld devices to fixed mount scanners, impacting how products are read and processed in the warehouse.
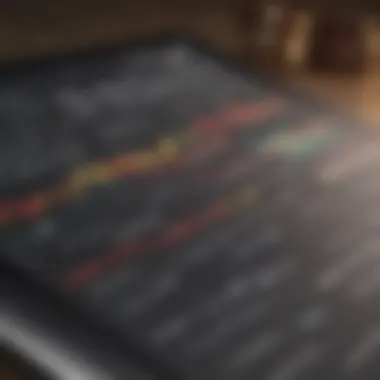
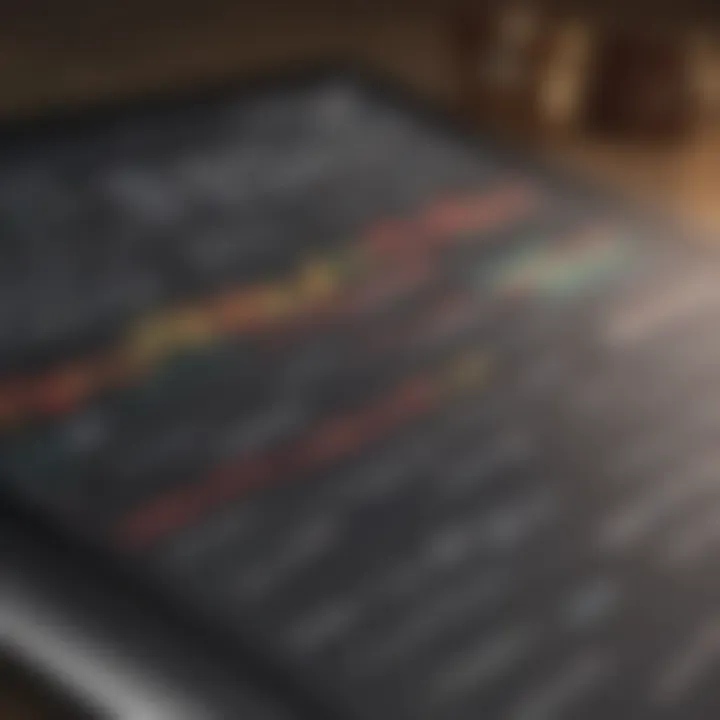
- Key Characteristic: The diverse types cater to various environments.
- Why Beneficial: Adaptabilityāwhether itās a busy retail flow or a sleepy warehouse, thereās a scanner that fits.
- Unique Feature: Some scanners now even include Bluetooth technology for wireless use, enhancing convenience.
The only thing that could be a bother is the initial investment cost; however, well-chosen scanners can drastically reduce labor hours and errors, streamlining the picking process.
Printers for Barcodes
Finally, consider printers for barcodes, which are a must for labeling items efficiently. These printers should be capable of printing durable barcodes that can withstand various conditionsālike humidity or temperature changes.
- Key Characteristic: The ability to produce high-quality, scannable labels.
- Why Beneficial: It enables businesses to quickly update and create labels on-site without additional outsourcing.
- Unique Feature: Some printers come with integrated systems that directly link to inventory software for real-time updates.
While dependable printing may come with its own costs, the agility it provides can certainly outweigh expenses in the long run.
Thoroughly assessing your needs and appropriately choosing both software and hardware can save you time, money, and headaches down the line.
Implementing Your Barcode System
Integrating a barcode system into your inventory management strategy is more than just slapping a few stickers on your products. This process can significantly enhance efficiency and accuracy in managing stock, ultimately benefiting your bottom line. By diligently implementing your barcode system, you essentially lay down the groundwork for streamlined operations that support sales professionals, entrepreneurs, and startup founders in making informed decisions.
Creating a Barcode Database
The first step in implementing your barcode system is establishing a barcode database. Think of this as the backbone of your inventory management. It's where all product information and barcode data come together. When you're setting it up, ensure that you include key details like:
- Product name
- Description
- SKU (Stock Keeping Unit)
- Price
- Quantity available
Creating this comprehensive database isn't just a formalityāit's crucial for maintaining an organized inventory. As the saying goes, "A stitch in time saves nine." Let this database do the heavy lifting in keeping track of your inventory, allowing you to identify trends or discrepancies before they snowball into larger problems.
Assigning Barcodes to Products
Once your database is established, the next logical move is to assign barcodes to each product. This task, while seemingly straightforward, requires attention to detail. Each item should have a unique barcode that correlates with its entry in the barcode database. Consider these points when assigning barcodes:
- Choose the right barcode type: Depending on your inventory's complexity or size, you might opt for one-dimensional or two-dimensional barcodes.
- Ensure legibility: The printed barcode should be easy to scan by various devices. A poorly printed barcode can cause headaches down the line.
- Stick to the plan: Once assigned, it's important to stay organized; keep track of what barcodes are used on what items to avoid overlaps.
Think of this as putting the right label on the right packageāmisplaced labels can lead to chaos in inventory management. The clarity brought by unique barcodes enhances operational efficiency and aids in tracking.
Testing Your System
After assigning barcodes, donāt just assume everything is in shipshape; itās time to put your system through its paces. Testing is an essential phase that helps you identify any flaws in your barcode setup before it goes live. Hereās how to do it:
- Scan barcodes: Use your scanning devices to see if they retrieve the correct product data from the database without hitches.
- Check database accuracy: Ensure that the product details pulled by the scanner match those in the database. This step will help catch any errors that could lead to stocking mistakes or financial loss.
- Simulate transactions: Conduct mock inventory transactions to gauge how well the system handles real-world scenarios. Look for any lag times or inaccuracies.
Itās crucial to catch potential issues now instead of later when your sales are on the line. As a wise person once said, "An ounce of prevention is worth a pound of cure." Make sure your system is rock-solid before rolling it out to your staff.
By effectively implementing your barcode system, you take a giant leap towards ensuring your inventory is as manageable and efficient as possible. As technology continues to evolve, those who embrace these tools will find themselves ahead of the pack, ready to scale their business without the weight of inefficient processes holding them back.
Training Staff on Barcode Usage
When introducing a barcode inventory management system, training the staff effectively can make or break the success of that system. This isn't just about showing them how to scan items; it's about cultivating a culture that embraces this technology. Proper training leads to accuracy, reduces errors, and enhances user confidence. Moreover, when employees understand the systemās importance and intricacies, they can leverage its full potential, which in turn streamlines operations and saves time and costs.
Developing Training Materials
To kick off the training process, developing comprehensive training materials is essential. These materials should cater to various learning styles, combining text, visuals, and hands-on demonstrations. A well-rounded approach accommodates everyone, from visual learners who benefit from infographics to kinesthetic learners who thrive in practical sessions.
- User Manuals: Create clear and concise user manuals that outline step-by-step procedures for scanning, inputting data, and troubleshooting common issues.
- Visual Aids: Develop chart or infographics that summarize key points, which staff can refer to easily when needed.
- Online Resources: Use platforms like Facebook groups or Reddit forums in your industry to provide a space for discussion. Link videos or articles that offer further insights about barcode technology.
These resources should be accessible. Whether printed or in digital formats, they should always be easy to find.
Conducting Hands-On Training Sessions
No one learns well from just reading manuals. Hosting hands-on training sessions can bridge the gap between theory and practice. This is where the rubber meets the road, enabling staff to engage directly with the barcode system.
During these sessions:
- Follow a Structured Agenda: Start with a short overview of the barcode system, explaining its relevance and benefits fostering buy-in. Then gradually move to the practical use of scanners and software.
- Interactive Exercises: Have employees work in pairs to practice scanning items and entering data. Practicing in a controlled environment will spark discussions around potential issues and solutions.
- Feedback Loop: Encourage participants to share their experiences and challenges. This feedback can guide additional training materials or help adjust processes for future training sessions.
- Set up real-life scenarios - for instance, inventory counts or restocking procedures using barcodes to make the process relatable.
Each session can vary depending on the depth of material needed, but fostering a collaborative environment allows deeper understanding and retention of knowledge.
Proper training not only improves system efficiency but boosts employee morale, knowing that they can operate confidently with the technology in hand.
Maintaining Your Barcode System
Maintaining your barcode system is something that often gets overlooked in the hustle of daily operations, but it's a critical component in ensuring efficiency and accuracy in inventory management. Just like a well-oiled machine that requires regular checks to operate smoothly, your barcode system requires routine maintenance to function at its best. The importance of this step cannot be overstated; neglecting it can lead to inaccuracies, stock losses, and a host of other complications that can ripple through your business.
Ensuring that your barcode system remains in top condition involves several factors, namely routine audits, maintenance, and timely system upgrades. This not only helps in keeping track of inventory levels but also improves staff productivity and customer satisfaction.
Routine Audits and Maintenance
Conducting routine audits serves as the backbone of a robust barcode system. It's your chance to give the system a thorough check-up. Imagine treating your system like a regular visitor to the doctor; keeping routine visits ensures everything remains in shape.
- Schedule Audits Regularly: Most businesses find it beneficial to schedule audits at regular intervals. This could range from monthly to quarterly, depending on inventory turnover rates. This helps catch discrepancies early, saving time and costs down the line.
- Check Scanners and Printers: Barcode scanners and printers can be the Achillesā heel of your system. A simple technical malfunction can cause setbacks. Regularly check their functionality to ensure they are operating as they should.
- Assess Data Integrity: Itās crucial to verify that the data entered into the system aligns with the actual stock on hand. Incorrect data can create a domino effect of issues with ordering and fulfillment.
- Feedback from Staff: Engage your employees in the auditing process. They are on the frontline and can provide valuable insights into any operational hiccups or functionalities that could use an upgrade.

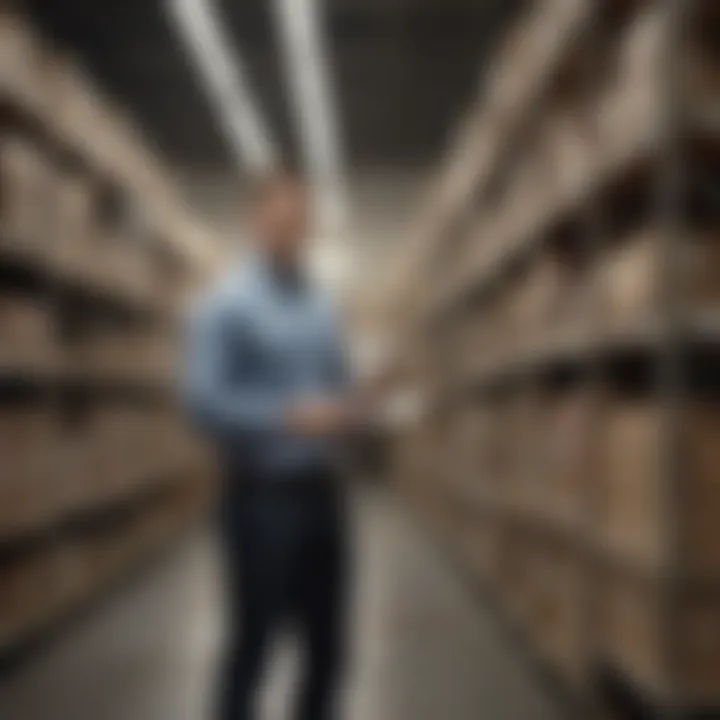
Routine audits not only ensure the longevity of your barcode system but also reinforce good practices among staff, providing an opportunity to address any concerns before they escalate. This proactive approach can set the stage for future operational success.
Upgrading Systems as Needed
Technology doesn't sit on its hands; it keeps evolving. Your barcode system should be flexible enough to adapt to these changes. Regular upgrades are non-negotiable if you want to stay ahead of the curve.
Here are some key considerations when thinking about upgrades:
- Assess for Compatibility: Before upgrading, ensure that any new software or hardware components are compatible with your existing setup. Compatibility issues can cause more harm than good, and you don't want to end up in a tangled mess of incompatibility.
- Stay Informed on Trends: Keep an eye on emerging technologies in the barcode domain. Whether it's the latest in scanning technology or developments in cloud-based inventory management, being proactive rather than reactive can save you from considerable headaches later.
- Invest in Training: With any upgrades, training is equally crucial. New features or updates might not deliver their full potential if your staff isn't educated on how to use them effectively.
- Evaluate Performance Metrics: Post-upgrade, take time to analyze performance improvements. Look closely at connection speed, data retrieval times, and user-friendliness. Reviewing these metrics will help you gauge whether the upgrade was a worthy investment.
Maintaining your barcode system isnāt a one-time task, but rather a continuous cycle of audits, maintenance, and upgrades. This consistent diligence not only prolongs the life of your hardware and software but also enhances overall efficiency. After all, in today's fast-paced world, running a tight ship can make the difference between losing or retaining customers.
Analyzing Inventory Data
Analyzing inventory data is a cornerstone of an efficient barcode inventory management system. When you have your barcodes in place, it's not merely about scanning and storing; itās about making sense of the data that comes flooding in. By analyzing this data, businesses can gain profound insights into their operations, improving overall efficiency and effectiveness.
When it comes to inventory analysis, capturing accurate data is like having a map before you embark on a trip. It guides your decisions and helps avoid potential pitfalls. Without this important piece, decision-making becomes guesswork, which is risky business for anyone looking to succeed. You might end up overstocking or, conversely, lacking critical items, driving losses or customer dissatisfaction.
Understanding Inventory Metrics
The data collected through barcode scanning provides various metrics that businesses use to make informed decisions. Primary among these are stock levels and turnover rates. Examining these metrics enables businesses to accurately assess their performance and respond to market demands swiftly.
Stock Levels
Stock levels represent the quantity of goods you have on hand at any given moment. Monitoring this metric is vital for maintaining balanced supply and demand. If stock levels are too low, you risk running out of products, leading to missed sales opportunities. On the other hand, having excess inventory ties up precious resources.
The importance of keeping an eye on stock levels cannot be stressed enough. They offer a keen insight into your purchasing patterns, customer demand, and overall inventory health. A notable feature of this metric is how it facilitates optimal ordering practices. Regularly analyzing stock levels allows you to realize trends, spot slow-moving items, and adjust inventory orders accordingly.
One drawback, however, is that if not monitored frequently, stock levels can rapidly become outdated, leading to misinformed decisions. Updating stock level data should thus be a routine task.
Turnover Rates
Turnover rates measure the speed at which inventory moves through your system. High turnover rates signify that your products are selling well, while low rates might suggest that items are stagnating on shelves. This factor speaks volumes about your inventory efficiency and market demands.
A key aspect of turnover rates is their direct connection to cash flow. When products move quickly, your capital is reinvested rapidly into new inventory, which is ideal for sustaining business growth. Furthermore, understanding turnover can pinpoint items that may need markdowns or promotions, increasing their appeal.
That said, caution is essential. Extremely high turnover can lead to stock shortages, thereby affecting customer satisfaction and incurring loss of sales. Balancing turnover should thus be a strategy within the greater inventory management control framework.
Utilizing Data for Business Decisions
Utilizing the data derived from analyzing your inventory is where intelligence transforms into action. Data interpretation and decision-making should go hand in hand. For instance, data-driven insights about stock levels can help steer your product assortment strategies.
Successful businesses approach inventory analysis as a regular part of their decision-making process. The use of analytics can help identify slow-selling items, assess seasonal trends, and optimize pricing strategies. Decreasing markdowns on slow items while boosting promotions for fast-moving goods ensures that each dollar spent is most effective.
Adopting data analytics tools can provide a deeper understanding of trends through predictive modeling, enabling businesses to foresee inventory needs accurately. By leveraging historical data, businesses can strategically plan for peak seasons and avoid last-minute surprises.
"Data is what you need to do analytics. Data is not a product, it is what analytics is based on."
Challenges in Barcode Inventory Management
Navigating the realm of barcode inventory management is not always smooth sailing. Despite the notable advantages it provides, several challenges can crop up that might hinder optimal performance. Identifying and addressing these issues is crucial for businesses aiming for efficiency and accuracy in their inventory control. The importance of this topic lies in recognizing that ahead of implementing a barcode system, one must understand potential roadblocks, ensuring a sound approach to mitigating them.
Common Issues Faced
Many businesses find themselves stumbling over common missteps in their barcode inventory management. Here are a few:
- Inaccurate Data Input: One of the primary concerns arises from human error during data entry. When product information is input incorrectly, it can cascade into larger mismanagement issues.
- Equipment Malfunctions: Scanners can be finicky. If hardware breaks down or becomes outdated, the entire system can falter.
- Integration Problems: Often, barcode systems are not seamlessly integrated with existing software and databases, leading to disparity in information.
- Staff Resistance: Employees may not be keen on adopting new technology, particularly if they donāt understand its benefits.
- Inventory Misalignment: Without a proper system to regularly update the inventory records, discrepancies can arise between actual stock and what's recorded.
These hurdles make it crucial for businesses to not only implement systems but to be aware of the frequent pitfalls that may accompany them.
Solutions to Overcome Challenges
Solving these challenges isnāt rocket science, but it does require a strategic mindset and some deliberate actions. Some effective solutions include:
- Thorough Training Programs: Emphasizing training can bridge the gap of understanding among staff. Create materials that explain how barcodes work and their significance to the workflow. Hands-on sessions can enhance familiarity.
- Regular Maintenance of Equipment: Scheduling routine checks on scanners and printers ensures they work efficiently and minimizes the risk of malfunction during crucial times.
- Robust Software Selection: Choose inventory management software that integrates well with existing systems, minimizing the chances of discrepancies. Before finalizing a selection, run tests to identify any potential integration issues.
- Data Validation Processes: Implement stringent data entry protocols. Use software that mitigates human error by incorporating validation checks to flag inconsistencies.
- Employee Engagement: Engage your employees in the process. Make them part of the solution by encouraging feedback about the barcode system and practicing changes suggested by the team.
"Understanding the challenges is half the battle. The other half is applying targeted solutions that pave the way for success."
By addressing these challenges methodically, businesses can streamline their barcode inventory management processes, leading to enhanced efficiency and accuracy. With the right tools and proactive thinking, overcoming these barriers can be much easier than it seems.
Future Trends in Barcode Technology
As we tread deeper into the 21st century, itās clear that barcode technology is not just hanging aroundāitās evolving. The evolution in this area happens rapidly, and grasping these trends equips businesses with foresight and adaptability.
Emerging Technologies
In the realm of inventory management, emerging technologies are shaking the old tree. Innovations like QR codes and NFC (Near Field Communication) are becoming increasingly pertinent. These technologies enhance data accuracy and boost consumer engagement. Imagine walking into a store and simply tapping your phone on a product to instantly access its details.
Moreover, RFID (Radio Frequency Identification) is gradually surging ahead as a preferred choice. Unlike traditional barcodes, which require direct line-of-sight for scanning, RFID works effectively when transmitting data without direct contact. This capability dramatically speeds up inventory processes, allowing for quicker stock audits and more streamlined operations.
Some of the noteworthy points to echo here include:
- Enhanced Data Capacity: New formats of barcodes, such as Data Matrix, can hold significantly more information than traditional UPC barcodes.
- Automation Compatibility: As businesses integrate automation, these new barcode systems align seamlessly, enhancing operational efficiency.
- Real-time Tracking: Emerging technologies facilitate real-time inventory tracking, which could ultimately thwart problems like overstocking or stockouts.
āIn an era where agility is critical, leveraging emerging technologies is not just an option but a necessity.ā
The Role of Automation
Automation has been a game-changer across industries, and barcode systems are riding this wave. The role of automation in barcode technology is paramount as it fosters faster, more accurate inventory management processes. Automated systems can regularly update inventory counts, minimizing human errorāa boon for any business owner.
A few key aspects of automation in barcode systems include:
- Inventory Updates: With an automated system, stock levels can adjust in real-time based on sales and returns, keeping the inventory data accurate round-the-clock.
- Operational Efficiency: Automation decreases the time spent on mundane tasks, such as data entry or manual stock checks, allowing personnel to focus on more strategic activities like sales or customer service.
- Integration with Other Systems: Modern barcode solutions often mesh well with ERP (Enterprise Resource Planning) systems. This harmonization enables businesses to maintain a cohesive operational flow that enhances overall productivity.
As automation continues its upward trajectory, the future of barcode technology seems bright. Simply put, evolving with these trends is sure to give business leaders a competitive edge, helping them navigate the bustling market landscape more proficiently.